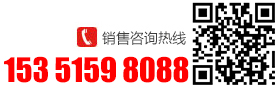
減速器傳動方案的設計 傳動比的確定 傳動比的確定主要是確定傳動比的大小。 混凝土攪拌車在作業(yè)和等待卸料過程中,通過取力器取出發(fā)動機的動力,將驅動液壓系統(tǒng)變量泵的機械能轉化為定量馬達。最后,減速器驅動攪拌筒裝置實施混凝土攪拌行為。 為了保證混凝土在攪拌過程中的質量,在運輸過程中,不僅要保證攪拌筒的轉動,還要控制精度,避免操作過程中的浪費。 在此期間,需要確定攪拌車的電機參數(shù),尤其是工作排量、持續(xù)壓力和峰值壓力。 要控制液壓馬達的轉速,一般要控制攪拌筒和減速器的傳動比。 傳動比的數(shù)值計算一般是根據(jù)運動中的有關原理和傳動的輪系在封閉系統(tǒng)中進行的。 確定參數(shù) 確定參數(shù)主要確定三種參數(shù)。首先,確定行星齒輪的數(shù)量,這與傳動比有關。 在動力傳遞過程中,行星齒輪數(shù)量越多,傳動優(yōu)勢越大。一般情況下,行星齒輪的數(shù)量會保持在2到5個之間。如果選擇行星齒輪的數(shù)量,會增加負荷分擔的難度。 而且增加行星齒輪的數(shù)量也會降低星架的剛度,從而制約實際的加工制造。 一般是在個別低速變速器中實現(xiàn)選擇更多的行星齒輪。 其次,確定齒輪的模數(shù)。首先,分析了行星齒輪的應力。根據(jù)減速器的實際使用情況,對減速器的受力部位進行了分析。 然后,分析了行星傳動齒輪強度設計的要點。根據(jù)行星傳動的結構特點和運動特點,掌握應力循環(huán)次數(shù)、動載荷系數(shù)和速度系數(shù)。 最后計算出每個檔位的模數(shù)。由于減速器易受沖擊載荷的影響,強度和韌性較高,在計算行星齒輪中輪系的模數(shù)時,應考慮齒根的彎曲疲勞強度。 第三,確定齒輪的齒數(shù)。在行星傳動設計中,齒輪齒數(shù)的確定主要分析傳動比的實際情況、同心情況、裝配情況和相鄰情況。 計算封閉式行星齒輪的傳動效率 影響封閉式行星齒輪傳動效率的主要因素有四個,其中之一是嚙合損失,主要是齒廓間摩擦產生的功率損失。 其次是軸承的摩擦損失,由于齒輪由安裝軸上的固定支架支撐,容易產生較大誤差。 三是水力損失,主要是齒輪嚙合傳動帶動潤滑油的攪動和飛濺造成的。 第四是封閉功率損失,因為封閉功率主要存在于輪系中,它不僅與傳動系數(shù)有很大關系,還與構件的摩擦速度和摩擦力有很大關系。 在計算閉式行星齒輪傳動效率時,首先要劃分傳動單元,然后分配傳動比,計算各支路的傳動功率。 選擇均載方式 由于行星齒輪傳動的體積小,承載能力高,造成這一特點的主要原因是多個行星齒輪分擔載荷,形成功率分流。 齒輪在實際傳動過程中,容易出現(xiàn)制造、裝配等誤差。 在減速機轉動過程中,減速機廠家采用的均載方式是行星架浮動方式。這種方法不需要設計支持,可以簡化結構,促進多級行星齒輪在傳動過程中的合理布局。
擺動機構的設計 擺動形式 減速器的擺動機構由調心軸承和圓弧齒擺動組成。這種結構的實施是通過連接齒輪和主軸承來完成的。在實際工作中,既能有效緩沖軸向力,又能改善浮動效果。 但由于鼓形齒輪的加工成本較高,這種結構的設計對設備的依賴性較高,需要單獨進行維修和更換。 對于法蘭擺動形式的輸出,該結構主要放在減速器的外殼上,既減小了減速器的體積,又與擺動結構融為一體,減少了零件數(shù)量。 為了減振和擺動,這種結構的設計為攪拌車等設備預留了較大的空間,可以滿足工作的實際需要。 回轉機構設計 回轉機構設計主要有三種類型。 一個是基球的擺動,主要是在減速器底部的支架上,隨著底座上的擺動球擺動。 這種回轉模式可以將減速器與回轉機構分離。如果某些零件損壞,不僅會影響整個減速機,也方便減速機廠家維修。 特別是對于曲齒的擺動,可以形成更大角度的擺動形式。 而且為了減小減速器的軸向尺寸,還可以為攪拌車上的其他部件提供更多的空間。 至于前支撐球的擺動,可以促進擺動角度,降低攪拌筒的重心。但由于支架是分體式結構,與螺栓結合牢固,容易導致支架與揮桿球的強度問題。 對于球窩擺動,這種結構省去了鼓形齒輪和調心滾子軸承的連接,不僅減小了減速器的軸向尺寸和重量,而且大大節(jié)省了成本,因此簡單的結構形式在維修過程中促進了更大的方便。
1。立磨減速機齒輪斷齒的特點 總的來說,立磨減速機齒輪斷齒的原因是多方面的。減速器廠家可以簡單總結為:非受力面高度低于受力面破碎高度。值得一提的是,如無特殊情況,輪齒斷裂多發(fā)生在螺旋錐齒輪上,損壞程度相對較輕。 但是,為了從根本上避免立磨減速機斷齒事故,必須找出其存在或潛在的因素,在提高其工作效率的基礎上,保證企業(yè)的經濟效益。 以軸向移動原因為切入點,軸承鎖緊螺母安裝不松動。修復后重新鎖緊螺母時,發(fā)現(xiàn)減速機現(xiàn)有速度比原來速度多了1200倍,節(jié)距為4mm。 換個角度說,原來的立磨減速機不可能也不會出現(xiàn)螺母不鎖緊的現(xiàn)象,因為經過了多道工序的檢驗。 是什么原因導致減速機斷齒磨損?引人深思 經相關工作人員仔細檢查,發(fā)現(xiàn)小齒輪的兩個肩部分別與軸套和軸承磨損,這是立磨減速機損壞的根本原因。 2。斷齒原因分析 立磨減速機斷齒原因可以簡單概括為三個方面:一是軸套與軸的配合有問題,簡單來說就是動配合。設備啟動時受多種因素影響,特別是慣性,使軸套與軸發(fā)生相對運動,造成立磨減速機斷齒。 其次,引進高科技設備,但相關工作人員操作技能差,導致開停磨次數(shù)增加,重復以往,造成設備故障。 最后,在生產過程中,或多或少會有軸向運動。設備啟動前,沒有全面檢查。此外,在操作誤差超過預期值后,突然振動值將停止。當磨機停止時,磨機上料層的厚度差會導致磨機反向運動。這些原因導致立磨減速機斷齒。
(2)降低人類研磨材料的粒度 在無特殊情況下,廠家將立磨最大給料粒度設計為80mm,也就是說,通過科學合理的方式降低給料粒度,可以提高立磨產量,在一定程度上降低生產能耗,為穩(wěn)定磨盤料層厚度創(chuàng)造條件,最終達到降低立磨運行中振動值的目的,保證相關設備的安全穩(wěn)定運行。 再者,如果條件允許,還要檢查其他嚙合的齒輪和軸承,然后才能制定出有效的方案。 抽出第一根傳動軸,排干潤滑油后,用窺鏡檢查減速機內軸承和行星齒輪的嚙合齒面,為設備的安全高效運行打下堅實的基礎。 (3)不定期對相關設備人員進行技能培訓,提高其專業(yè)技能。 當然,這需要相關管理人員根據(jù)立磨減速機的日常情況,或者整個設備的情況,不定期的對相關設備操作人員進行培訓,保證其專業(yè)技能能夠高水平的滿足設備運行的需要。另一方面,采用這種方法可以降低設備的磨損程度,減少設備故障的概率,為其高效穩(wěn)定運行創(chuàng)造條件。 再者,對相關設備工作人員的技能培訓不僅可以更新他們的工作理念,還可以幫助他們將所學應用到實際過程中,不僅提高了他們的專業(yè)技能,也穩(wěn)步提高了他們的專業(yè)素質。
目前應用最廣泛的中小功率硬齒面減速器有斜齒輪同軸減速器、斜齒輪傘齒輪減速器、平行軸斜齒輪減速器和斜齒輪蝸輪減速器。它們在減速機行業(yè)被稱為四大系列減速機,其特點是高度模塊化設計,通用性強(除非本文另有說明,減速機均指四大系列減速機)。 減速機在使用過程中,漏油是一個常見的問題,漏油對減速機的危害很大。 首先,漏油使減速器潤滑油油位降低,造成齒輪嚙合面和軸承滾道磨損更嚴重,效率降低,溫度升高,導致減速器失效;其次,即使減速器暫時不出故障,漏油也會造成潤滑油的浪費和環(huán)境污染。 因此,減速器漏油是減速器生產廠家需要重視和解決的課題。 主要對四大系列減速器經常出現(xiàn)的幾種漏油現(xiàn)象進行分析研究,從工藝改進和結構優(yōu)化方面提出改進對策和解決方案。
齒輪箱結構刀架箱內部需要四級減速,以降低速度,增加扭矩。 制造商有幾個問題需要解決。首先,齒輪的相關精度保證增加了裝配過程的復雜性。 其次,刀架分度過程中容易產生噪音,因為各級內齒圈和雙聯(lián)齒輪的加工精度不易保證。 減速器結構刀架可以解決以上問題。 該刀架減速器一般由供應商提供,減速器輸出齒輪軸的標準間隙為12 & prime 經過現(xiàn)場測試和基準測試,實現(xiàn)了鎖緊過程無校正,分度過程無噪音。 通過對減速器結構立式伺服數(shù)控刀架的設計研究,將刀架設計過程、刀架理論分析、有限元分析、實驗過程以及與其他刀架結構的比較結合起來。 該刀架結構合理,性能優(yōu)越,是立式數(shù)控車床的可靠解決方案。
1。齒輪總成調整不當 觀察損壞的齒輪。大部分輪齒在支承面同一側的近端都有或大或小的凹坑,但在輪齒中間到另一端沒有發(fā)現(xiàn)凹坑,這說明齒輪裝配時兩齒輪軸之間存在平行度誤差,導致輪齒在整個齒寬上受力不均勻& ldquo摸一頭& rdquo現(xiàn)象,以至于在某些區(qū)域存在應力集中。 2。重載大負荷波動 減速機連接擠出機熔融泵,用于對熔融樹脂加壓,屬于低速重載減速機。 由于熔融泵的介質是各種不同品牌的樹脂,樹脂的熔融指差異很大,導致減速機的傳遞扭矩變化很大。 2003年對擠出機進行了擴能改造,整機生產能力從13.3 t/h擴大到15.5 t/h,但這個減速機沒有改造,減速機廠家一直讓設備滿負荷甚至超負荷運轉。以上因素都容易造成齒輪疲勞裂紋。 3。齒面熱處理不當 經檢測,輪齒工作面硬度約為HRC45,齒頂面硬度為HRC53。齒面硬度明顯低于齒頂,可能是齒面磨損的原因。 對于重載齒輪,硬度通常應在HRC56以上,這樣才有更好的耐磨性和抗疲勞性。 相比較而言,這種齒輪的硬度明顯偏低,在應力集中部位容易出現(xiàn)點蝕。
修復工藝 焊接工藝 為了保證齒輪表面的硬度,防止齒輪產生較大的熱變形,選擇了冷焊工藝。 所謂冷焊,就是焊前不預熱,焊后不保溫,小參數(shù)焊接。 焊接方法:氬弧焊。 焊絲:12CrNi德國制造,& phi1.2毫米 焊接電流:70A 焊接注意事項:間歇焊接,控制焊接溫度,不要過熱。 修復工藝 (1)清理裂紋,打磨焊接面。 裂紋清理前,齒圈端面應用30mm厚鋼板剛性固定,以減少日后施工時的變形。 使用& phi2.0毫米碳弧氣刨清理所有裂縫。 氣刨時,宜采用小電流、間歇式施工,以減少變形和熱影響區(qū)。 裂紋去除后,用手磨機打磨修整。打磨的目的是磨掉碳平面的氧化層和熱影響區(qū),約1.5mm厚。 清理磨削裂紋時,要注意保留齒頂和齒根未損壞的部分作為修復的基準面。 拋光后,進行污點檢測以確認沒有殘留裂紋。 (2)焊接齒輪齒 由于焊接量大,為了減小焊接應力和變形,應采用多道、多層、多段間歇焊接方法。 從開裂的殘齒開始焊接,焊接齒圈底部。焊接后,檢查焊縫,確保沒有裂紋。 焊完底部后,沿齒高逐層焊接,直至焊完整個齒。 制造商應嚴格按照焊接工藝焊接減速器,并嚴格控制焊接熱影響區(qū)的電流和溫度。
(3)焊接加強板 考慮到腹板開裂側的應力較大,制造商在齒圈的下腹板上焊接了加強板,以加強齒圈的強度。 (4)粗磨齒輪 在焊接齒輪的同時,根據(jù)齒輪的相關參數(shù)制作齒形樣板,以便磨削齒輪時檢查齒輪的形狀。 齒形模板采用線切割加工。為了確保焊接的新齒和相鄰齒之間的相對位置,齒形模板必須跨越三個齒。 粗磨可以用粗砂輪手動完成,在磨削過程中使用齒廓模板作為參考。 (5)研磨齒輪 使用細粒砂輪進一步研磨齒輪。磨削時以齒形樣板為基準,在齒輪上涂上藍鉛,檢查齒輪與齒形樣板的配合。 磨削齒輪時,注意檢查新焊齒兩側的相鄰齒輪。 由于焊接過程不可避免地會引起熱變形,相鄰齒的位置會略有變化。如果發(fā)現(xiàn)鄰齒變形,應先打磨鄰齒,以免影響新齒的齒廓檢查。 齒形檢查見圖5。 磨齒后測得的齒面硬度為HRC 42 ~ 46,硬度較低。 (6)裝配修改 通過磨削齒輪,齒輪具有基本的外部尺寸。為了使齒面的實際接觸條件滿足要求,需要對齒輪進行修形。 將修復后的齒輪裝配到齒輪箱上,涂上紅丹檢查齒輪工作面的接觸情況,用手磨去除影響接觸的高點。
減速器的噪音原理 減速器的噪音一般是由齒輪的摩擦或齒輪的碰撞或運轉時的振動引起的。 減速器的噪音與其自身結構有關。 其中,關系最密切的是齒輪的設計方法和齒輪的加工精度。 具體來說,首先,行星齒輪和太陽齒輪在齒輪運轉中起著關鍵作用。 齒輪運行過程中,內齒圈嚙合,但持續(xù)的沖擊使齒輪產生嚙合頻率,在受迫條件下實現(xiàn)受迫振動。 其中,齒輪的嚙合頻率,F(xiàn)Z=nZ/60,由這個公式,減速器廠家知道,在轉速高的情況下,齒輪的嚙合程度也提高了,噪音也降低了;其次,齒輪的加工精度和表面粗糙度也是產生噪音的主要原因。 在齒輪的加工中,要從這兩個方面入手,加強齒輪精度的加工。 最后,齒輪不斷相互摩擦,齒輪振動,產生噪音。 加工精度是確定噪聲值的決定性因素。 齒輪減速器的主要功能是傳遞轉速和扭矩,因此,齒輪的加工精度要求齒輪的穩(wěn)定性。 穩(wěn)定性更高的齒輪,一方面延長了使用壽命。 在傳動過程中,有效降低了沖擊和振動,也降低了噪音。
齒輪狀況對噪聲的影響 基于減速器齒輪運行的原理,減速器廠家可以有效結合行星結構,實現(xiàn)對各種類型減速器的統(tǒng)計和分析。 顯然,減速器的噪聲主要是由齒輪嚙合引起的。 如果我們優(yōu)化齒輪參數(shù) 可以降低減速器的噪音。 1。精度影響 在加工精度上,等級決定了齒輪的性能。 在嚙合的過程中,產生的噪音也是由此決定的。 設計人員在設計齒輪減速器時,以性價比為出發(fā)點,確定更經濟實用的齒輪,選擇加工精度等級。 這樣就忽略了齒輪加工精度水平對噪聲水平的影響[2] 通過實驗研究,加工精度高的齒輪噪聲遠低于加工精度低的齒輪。 因此,在條件允許的情況下,選擇高精度的齒輪加工可以降低齒輪噪聲。 2。結構影響 在設計減速器齒輪時,當齒輪寬度增大時,在扭矩不變的情況下,各齒輪的單位載荷減小。 此時齒輪重合度增大,因此齒輪變形減小,從而改善齒輪傳動。 噪音相應減少。 德國機械設計專家Opaz的研究表明,在一定條件下,當扭矩不變時,大齒寬產生的噪聲小于小齒寬產生的噪聲。 小齒距可以保證多齒接觸。
提高內齒輪的精度 1。提高準確率?,F(xiàn)有的齒輪大多是硬齒面齒輪 。在提高加工精度方面,減速器制造商主要采用磨齒技術。 在表面粗糙度方面,為了實現(xiàn)磨齒技術,可以大量進口設備,設備的技術水平也較高。 其中,霍夫勒H40O,德國,或德國和H80O成型軋機是一些最好的選擇。 在先進設備的試用下,齒輪的精度水平可以提高。 更高的加工精度可以提高工作穩(wěn)定性。 穩(wěn)定性的提高可以減少不必要的振動。 從而降低噪音。 在設計允許的條件下,應選擇較高的齒輪加工精度等級。 2。提高粗糙度 提高齒輪的表面粗糙度。 磨齒時,輸入齒輪參數(shù)。 修整齒輪的輪廓 磨齒后齒輪精度提高,等級提高,精度等級達到五級。 在提高加工精度的同時,有效降低了齒輪嚙合過程中的噪聲。 硬齒面是齒輪的特點。 磨削后,齒輪的表面粗糙度將高于Ra0.8 當摩擦系數(shù)降低時,噪音也降低。 這兩種關系是一種近似的線性遞增關系[3] 在不同齒面粗糙度的齒輪中,噪聲的聲級約為4db。為了滿足切邊和齒向的要求,必須經過齒輪檢測中心的檢測。 在齒輪精度和齒輪齒向方面,符合相關標準。 一般來說,磨齒后齒面粗糙度提高,噪音降低。 3。齒輪結構調整 根據(jù)低噪聲的要求,齒輪結構也是齒輪設計的關鍵步驟。 在設計時,通過增加齒輪的齒寬,減小齒輪齒距的壓力角,修整齒輪齒頂?shù)牡菇?,通過全面合理的選擇實現(xiàn)齒輪變位系數(shù),最終完成齒輪結構設計。
RV減速器是在擺線針輪的基礎上發(fā)展起來的一種新型傳動機構。 它具有體積小、重量輕、傳動比大、效率高等一系列優(yōu)點。與傳統(tǒng)的擺線針輪行星傳動機構相比,它具有更小的體積、更大的剛度和過載能力,抗沖擊能力也提高了很多。因此,它被廣泛應用于數(shù)控機械行業(yè),尤其是工業(yè)機器人領域。 國內外許多學者對RV減速器做了大量的研究,主要集中在動態(tài)性能、傳動精度和改型優(yōu)化方面,包括RV減速器的動力學建模方法、固有頻率研究、剛度計算和虛擬樣機仿真技術;研究傳動誤差曲線,分析計算RV減速器的側隙;提出了不同的改型優(yōu)化方案,以提高減速器的運動精度和傳動效率,保證其具有較小的側隙、較高的剛度和承載能力。 在上述研究中,有學者做了有限元分析,但只是簡單地提取齒面上的應力值來驗證模型的正確性,這是研究修形和誤差的前提。 也有學者對擺線齒輪針齒傳動部分的齒面接觸進行了重點研究,但將擺線齒輪針齒模型簡化為平面問題,忽略了齒面接觸面積的變化,不能完全反映齒面的實際接觸情況。而且減速器廠家還沒有研究過嚙合力、接觸應力、接觸面積在單個齒面上和嚙合過程中的分布和變化規(guī)律。
減速器廠家在ANSYS中建立了擺線輪和針齒的三維嚙合模型。通過對參與嚙合的19個擺線輪的嚙合力、最大接觸應力和齒面接觸面積分布的分析,選取了傳動過程中擺線輪和針齒的6個嚙合角。得到了各嚙合角下擺線輪齒面嚙合力、最大接觸應力和接觸面積的變化規(guī)律: (1)理論分析表明,有限元計算結果對應的擺線輪齒面嚙合力和接觸應力曲線具有相同的變化趨勢,均在第四齒處達到峰值。 (2)按照平行齒寬方向和垂直齒寬方向提取的齒面數(shù)據(jù)曲線反映出擺線輪與針齒的嚙合區(qū)域近似為鼓形,即條紋外接觸應力小,內接觸應力大,兩端接觸應力小,中間區(qū)域接觸應力大。 (3)擺線齒輪旋轉6個角度時,對應的19個擺線齒輪齒面上的最大接觸應力在每個旋轉角度的變化趨勢是一致的,峰值出現(xiàn)在第4個齒附近。 在不同的旋轉角度下,嚙合19對齒,嚙合齒數(shù)與嚙合齒數(shù)相等。 對于某一齒從嚙合到嚙合,其齒面上的最大接觸應力先增大后減小,其接觸面積在傳動過程中也從齒根方向向齒頂方向偏移。
改進的中心傳動磨機減速器均載結構 在廠家改進的兩級中心傳動磨機減速器的均載結構中,一級齒輪軸同時與兩個一級齒輪部件嚙合,兩個一級齒輪部件的空心軸通過鎖緊盤連接到軟軸的一端,兩個二級齒輪軸通過鎖緊盤連接到軟軸的另一端,兩個二級齒輪軸同時與輸出軸上的二級齒輪嚙合。調整載荷分配時,確保第一齒輪軸5同時與兩個第一齒輪1嚙合,當兩個第二齒輪軸8同時與第二齒輪7嚙合時,擰緊所有鎖緊盤,實現(xiàn)載荷分配。 改進型中心傳動磨機減速器的優(yōu)點 改進后的兩級中心傳動磨機減速器工藝簡單,減少了60個大尺寸銷孔的配套。由于取消了軟軸和二級齒輪軸的連接法蘭,節(jié)省了原材料的消耗;精度容易保證,裝配后的二級齒輪軸節(jié)圓跳動小于0.05 mm,均載效果好;在以后的設備維護和更換中,如齒輪或齒輪軸,不需要預先裝配、調整載荷分配和匹配連接銷孔。齒輪或齒輪軸可直接制成成品,然后安裝、調整和固定,便于安裝、使用和維修。